¿Qué es un Sistema SCADA? El Corazón de la Automatización Industrial
Aprenda qué es un sistema SCADA, cómo funciona, sus componentes, beneficios y cómo los SCADA en nube están impulsando la industria 4.0
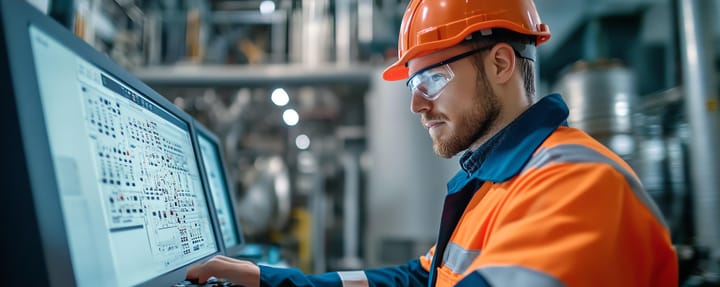
SCADA , abreviación para el control de supervisión y la adquisición de datos, es el centro de la industria moderna. dashboard en tiempo real que observa cada válvula, motor y sensor en el piso de su planta y le permite actuar para prevenir paros.
En esencia, un sistema SCADA vincula los dispositivos de campo (a través de PLC o RTU) a un servidor central, ahora cada vez más en la nube, donde los datos se almacenan y visualizan en vivo, y se convierten en ideas tangibles. Los operadores ven temperaturas, presiones y recuentos de producción, ajustar puntos y activar alertas mucho antes de que una falla cueste dinero.
¿Por qué importa eso en 2025? Porque los problemas de la cadena de suministro global, los costos de energía y las reglas de seguridad más estrictas dejan cero espacio para las conjeturas. SCADA bien ajustada ayuda a los equipos a sacar más rendimiento de activos en envejecimiento, reducir los paros no planeados y respaldar cada decisión con datos. Y con SCADA basado en la nube , ya no necesita racks de servidores o una VPN para mantener sus ojos en sitios remotos; solo un navegador seguro...y un buen café.
En esta guía aprenderás:
- Cómo SCADA evolucionó desde los mainframes de la década de 1970 hasta IoT .
- Componentes esenciales : sensores, PLC, HMI, bases de datos) y cómo encajan.
- Las plataformas SCADA vs. DCS vs. IoT para que pueda elegir lo que realmente se ajusta a su planta.
- Casos de uso del mundo real en energía, agua y alimentos y bebidas que prueban el ROI.
¿Listo para levantar el capó de la tecnología que mantiene las fábricas, las tuberías y las redes eléctricas que tararean? Vamos a sumergirnos directamente.
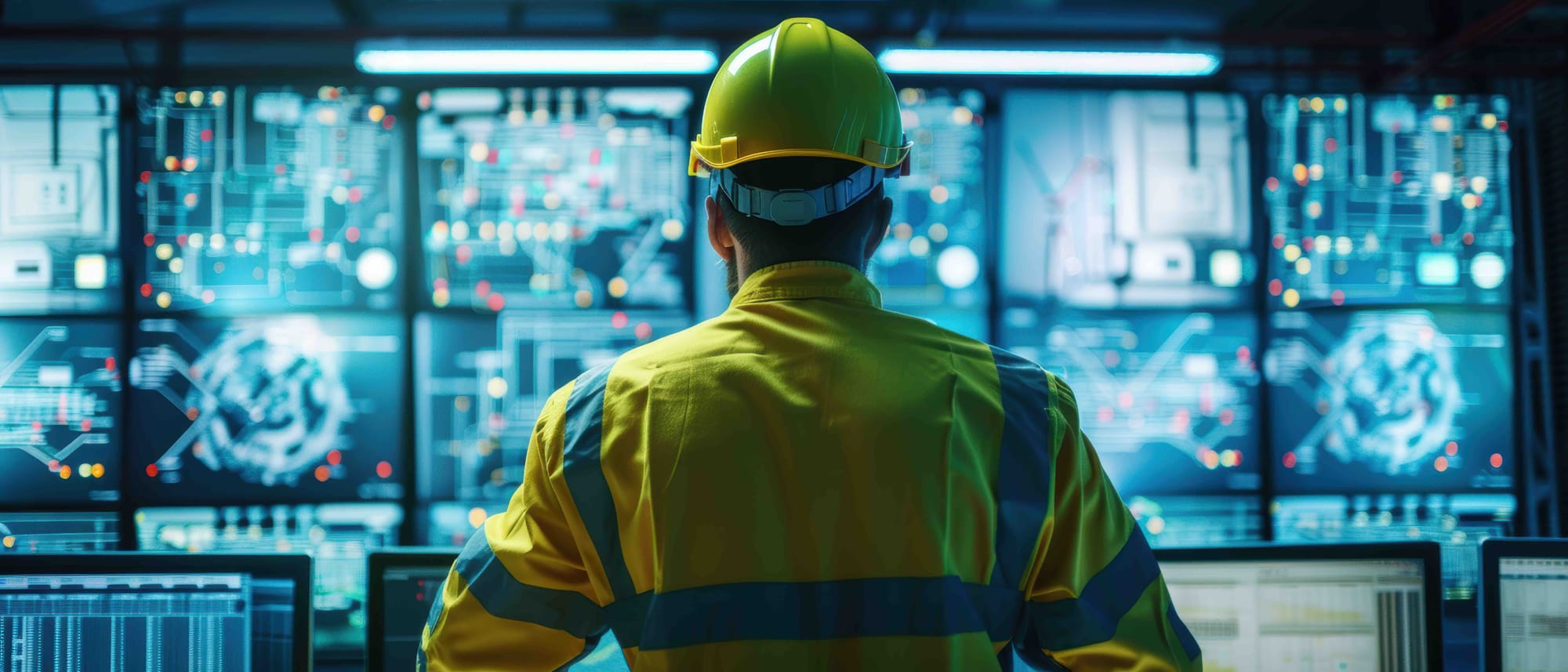
¿Qué es SCADA?
SCADA significa control de supervisión y adquisición de datos, un término técnico que se ha convertido en la línea de vida de la automatización industrial moderna, un sistema de control compuesto por componentes de software y hardware que le brinda un control total sobre su operación.
En esencia, los sistemas SCADA se comunican directamente con la maquinaria de la planta, recopilando datos en tiempo real y poniéndolos a disposición de su equipo. Puede ver el rendimiento del equipo, analizar tendencias de datos y detectar ineficiencias antes de que se conviertan en problemas importantes. Los sistemas SCADA también facilitan la recopilación de datos y la toma de decisiones en tiempo real, lo que los hace esenciales para gestionar equipos de control en ubicaciones remotas y mejorar la automatización y la eficiencia en las operaciones industriales. ¿El resultado? Más eficiencia, menos cuellos de botella y decisiones más informadas que impactan sus resultados. No se trata sólo de mantener las ruedas girando, sino de optimizar cada engranaje de la máquina.
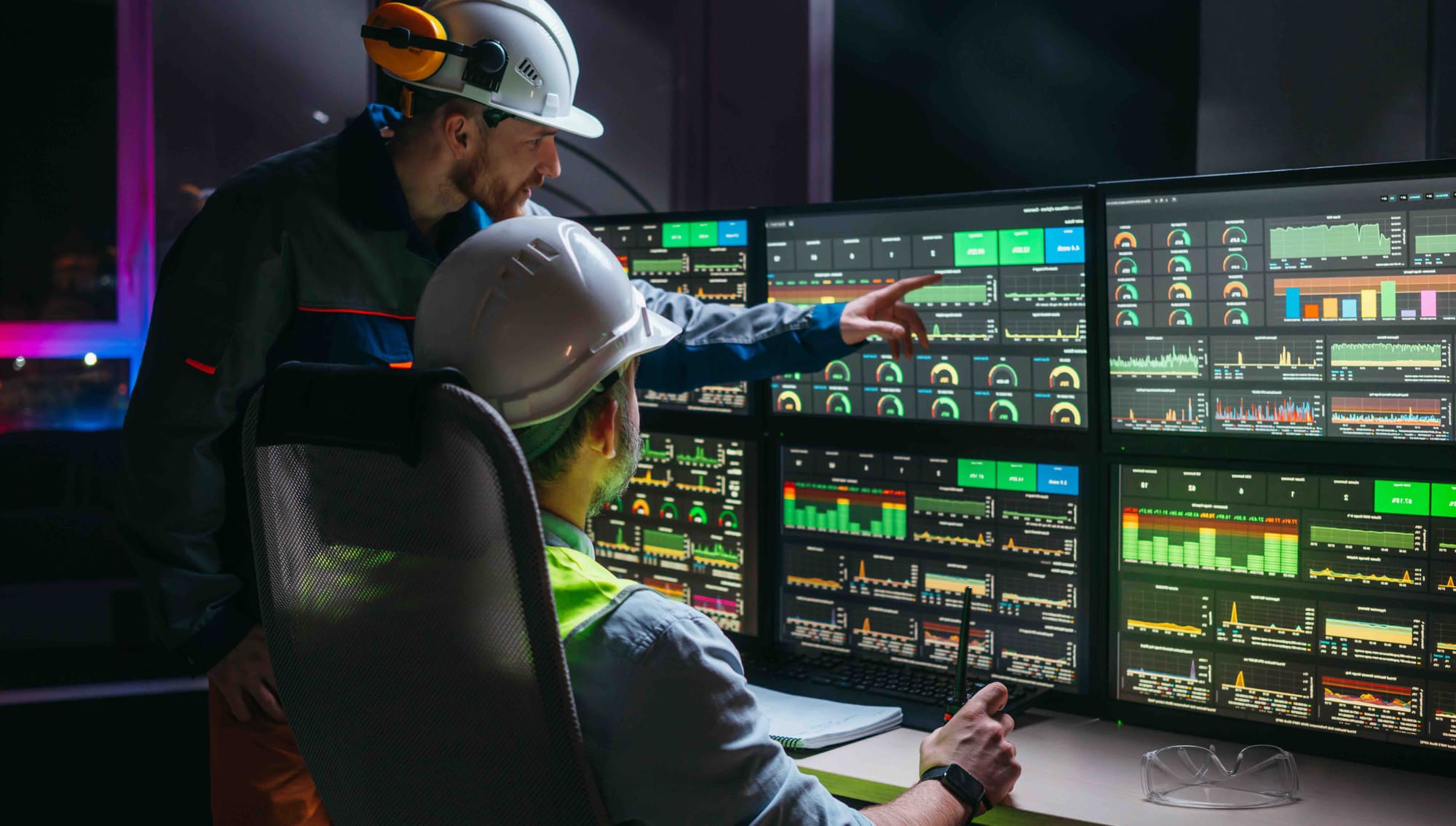
SCADA comienza en la columna vertebral: el controlador lógico programable (PLC) que recopila datos de sensores y dispositivos de toda la planta. Estos PLC son los traductores y se comunican con objetos como máquinas de fábrica, HMI (interfaces hombre-máquina) y varios dispositivos finales. Recopilan datos críticos (temperatura, presión, velocidad y más) y los envían de regreso a un sistema central donde se pueden monitorear, analizar y actuar en consecuencia.
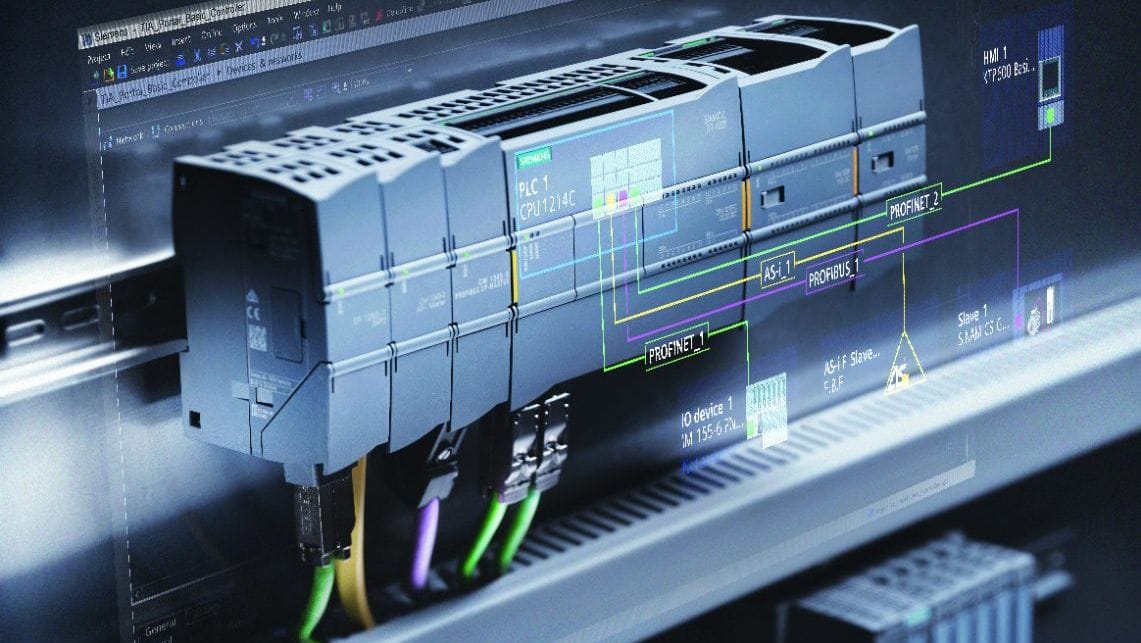
Este nivel de granularidad es lo que hace que SCADA sea tan esencial. No solo le permite ver lo que sucede en sus procesos, sino que también le brinda información para predecir los problemas antes de que se conviertan en tiempos de inactividad.
Historia y Evolución de SCADA
La historia de SCADA comienza a principios de la década de 1970, cuando la fabricación atravesaba una importante transformación. Durante este período nació el término SCADA y con él la tecnología que cambiaría la forma en que monitoreamos y controlamos los procesos industriales. En aquel entonces, todo comenzó con las computadoras centrales, máquinas enormes que eran el sistema nervioso central de los primeros sistemas SCADA . Estos mainframes permitieron a las empresas automatizar algunas funciones básicas y recopilar datos críticos, pero aún eran torpes y limitados por la tecnología de la época.
Primera generación
SCADA monolítico: Los primeros sistemas SCADA se construyeron en computadoras centrales donde todo el procesamiento se realizaba en una sola máquina. Los datos se recogieron, almacenaron y procesaron dentro de la computadora central y no había conectividad en red entre los diferentes sistemas. Estos sistemas SCADA monolíticos eran autónomos y el alcance de la automatización se limitaba a los límites físicos de la instalación.
En este punto, la única forma de controlar (y supervisar) la maquinaria era mediante el uso de circuitos de relés electromecánicos; cada motor o actuador tenía que encenderse o apagarse individualmente. Esto dio lugar a que las fábricas necesitaran grandes armarios llenos de relés de potencia.
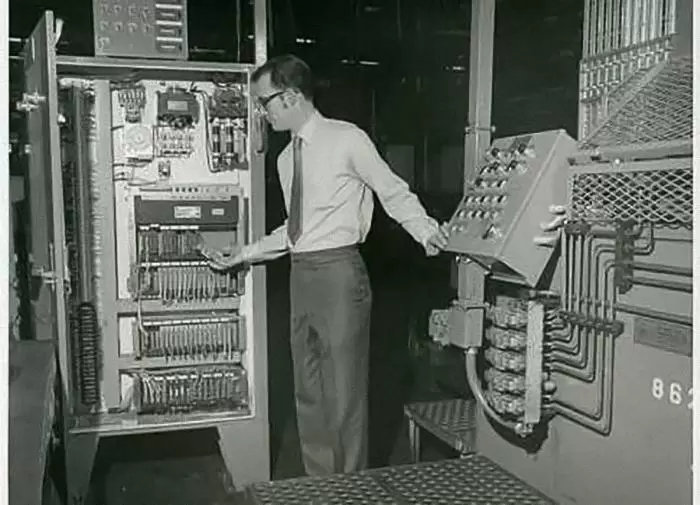
Segunda Generación: El nacimiento de los PLC
Luego vinieron los microprocesadores y los controladores lógicos programables (PLC) a mediados y finales de los años 70 y nació una nueva ola de automatización. La capacidad de unificar el control de procesos a través de PLC allanó el camino para los sistemas de supervisión centralizados y el panorama SCADA comenzó a cambiar. En las décadas de 1980 y 1990, SCADA evolucionó aún más con el desarrollo de la tecnología de redes de área local (LAN) y la aparición del software de interfaz hombre-máquina (HMI) basado en PC. Estos sistemas SCADA distribuidos redujeron la huella del hardware y aumentaron las capacidades de comunicación para que los sistemas pudieran volverse más modulares, escalables y fáciles de usar. Los operadores ahora podían controlar operaciones complejas de la planta desde computadoras de escritorio. Desde entonces, han surgido sistemas SCADA modernos que permiten el acceso a datos en tiempo real, una integración mejorada con otras infraestructuras de TI, como bases de datos SQL, y ofrecen mejoras significativas en eficiencia, seguridad y confiabilidad.
Tercera Generación: Sistemas SCADA en red
En los años 90, SCADA comenzó a aprovechar las redes de área amplia (WAN) y podía comunicarse a largas distancias. Estos sistemas SCADA en red adoptaron una arquitectura de sistema abierta y protocolos de comunicaciones estándar, lo que permitió la interoperabilidad entre dispositivos de diferentes proveedores. Esto fue un gran problema para industrias como la energía, el petróleo y el gas, que necesitaban monitorear líneas eléctricas o tuberías vastas y remotas. Ahora se podrían enviar datos a salas de control alejadas del lugar de operaciones y centralizar el control de los sistemas distribuidos.
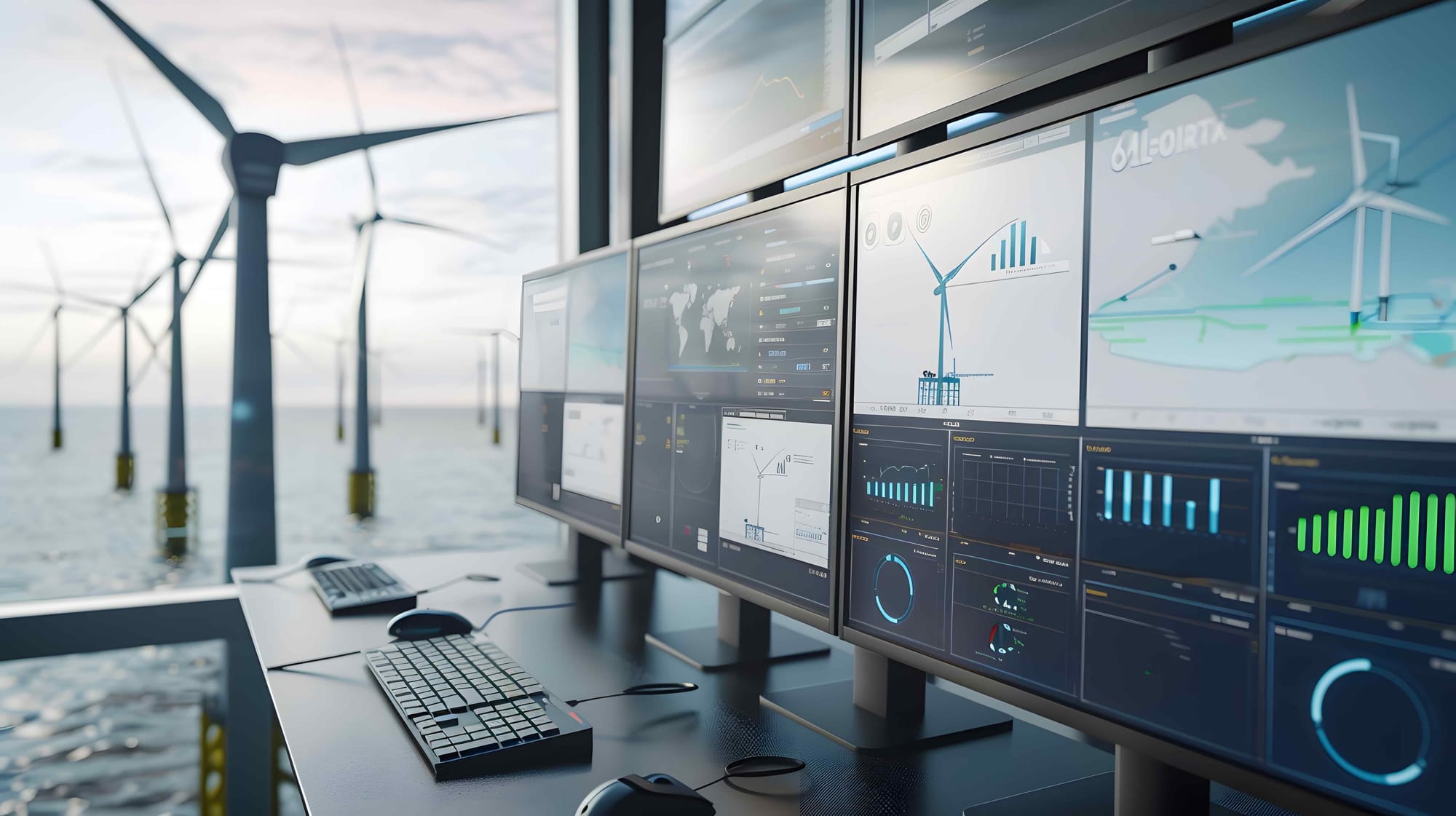
A medida que entramos en el siglo XXI, los sistemas SCADA adoptaron el análisis de datos en tiempo real, la computación en la nube y la conectividad global. Los sistemas actuales están muy lejos de los mainframes de antaño, con datos que fluyen desde la planta hasta las salas de control (y más allá) en tiempo real. De hecho, las plataformas SCADA modernas permiten el monitoreo remoto desde cualquier parte del mundo, ya sea que esté en su escritorio o en movimiento. Por lo tanto, los gerentes de confiabilidad ya no tienen que estar atados a sus estaciones de trabajo para mantener el pulso de sus operaciones. Con unos pocos clics pueden ver el estado del equipo, diagnosticar problemas y tomar decisiones sobre la marcha.
La próxima evolución de los sistemas SCADA
La próxima evolución de los sistemas SCADA está determinada por el auge de las plataformas SCADA y IIoT basadas en la nube. Estas tecnologías están permitiendo un cambio de sistemas tradicionales locales a soluciones más flexibles, escalables y remotas. SCADA basado en la nube permite acceder a datos en tiempo real desde cualquier lugar, ofreciendo visibilidad y control de las operaciones sin precedentes. Junto con las plataformas IIoT , que integran una amplia red de sensores y dispositivos inteligentes, los sistemas SCADA se están volviendo más conectados y ricos en datos. Esta evolución proporciona a las industrias una visión más profunda de sus procesos, lo que permite una toma de decisiones más rápida y una gestión proactiva de equipos y recursos, al mismo tiempo que reduce los costos de infraestructura y mejora la eficiencia operativa.
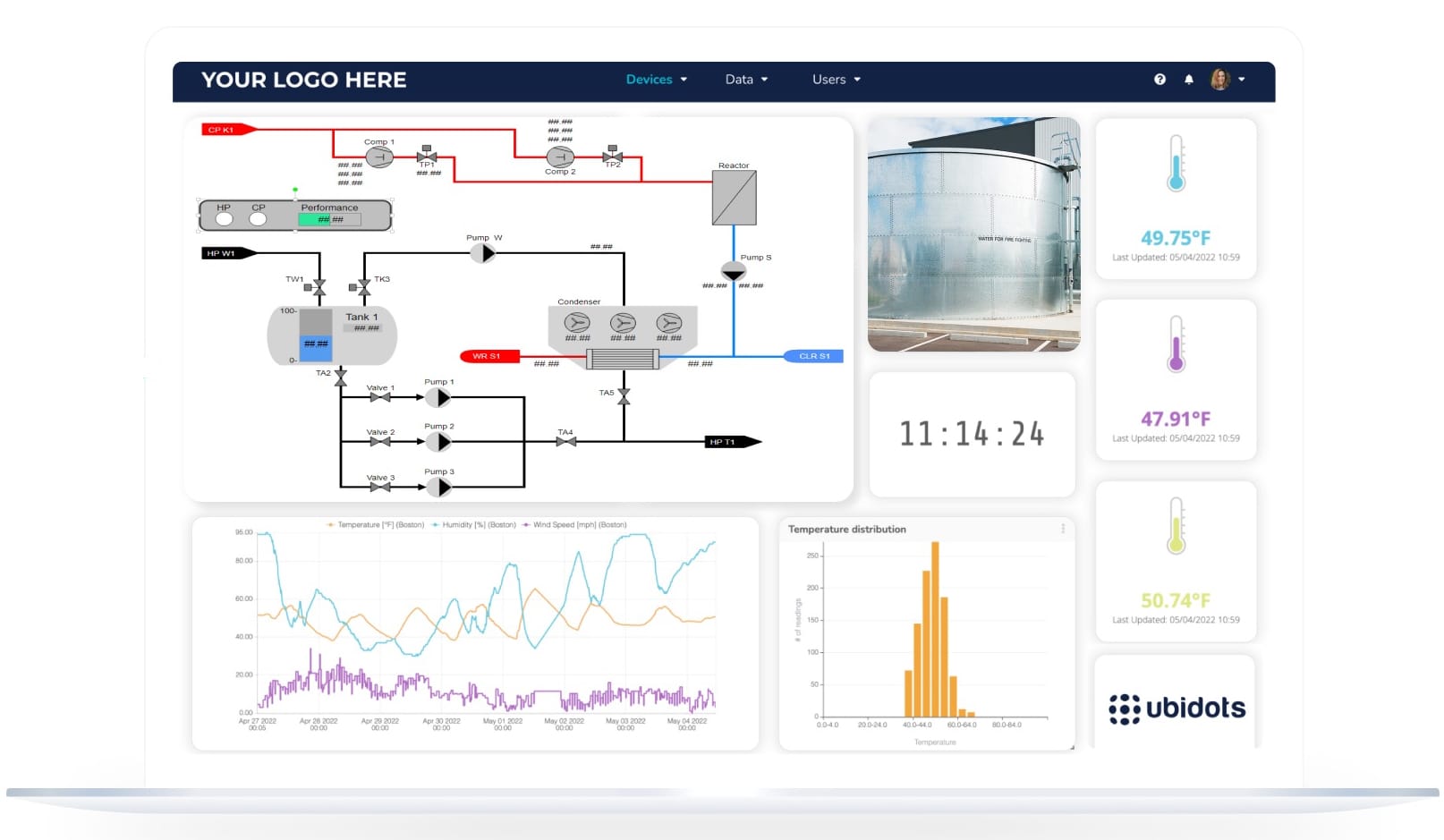
Componentes SCADA
En el corazón de cada sistema SCADA se encuentran sus componentes, cada uno de los cuales desempeña un papel fundamental en el control y monitoreo de procesos industriales complejos. Estos componentes trabajan juntos para brindar a los gerentes de confiabilidad visibilidad y control total de sus equipos a kilómetros de distancia:
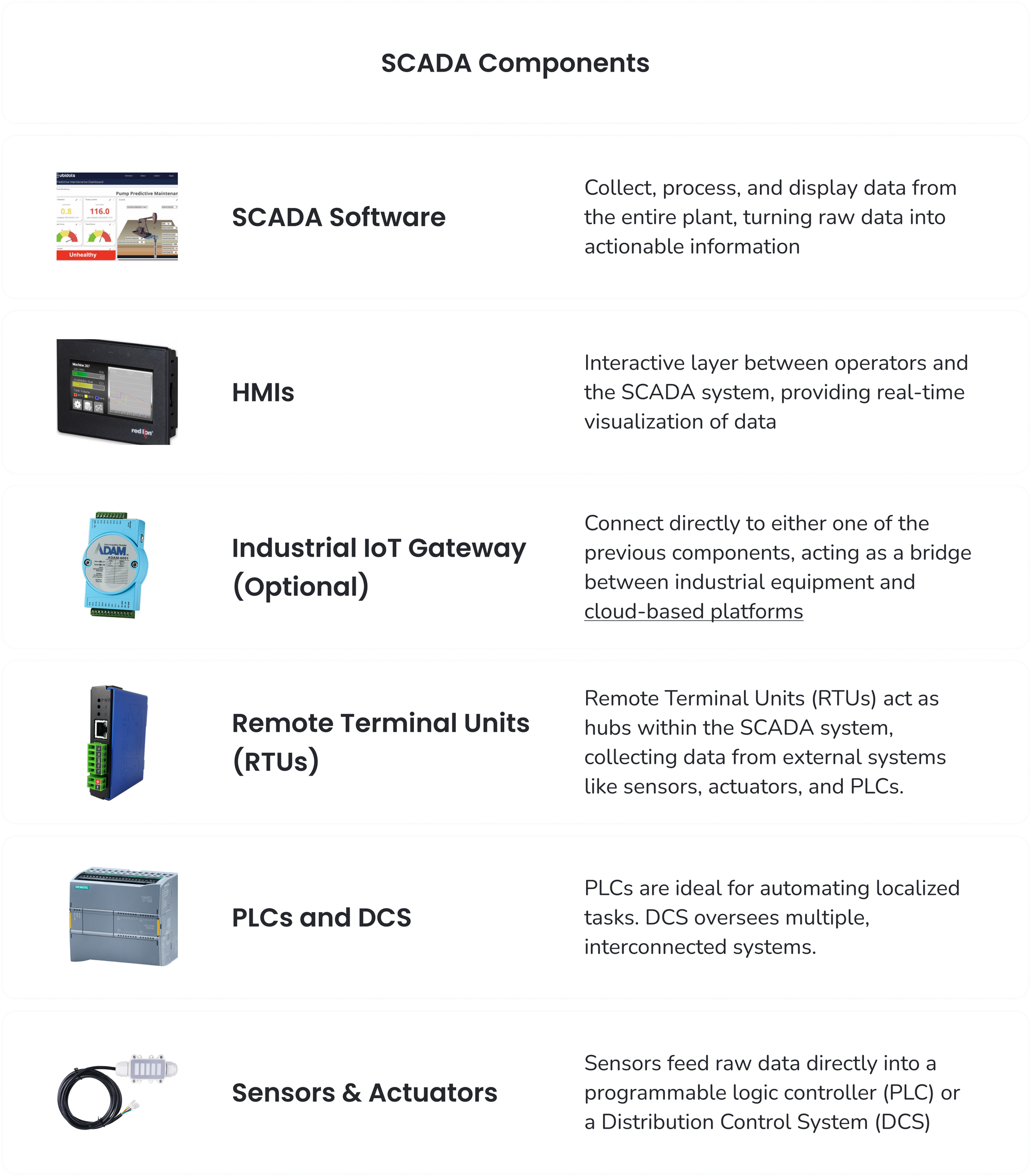
1- Sensores y Actuadores
Todo comienza en el terreno con sensores y actuadores. Ya sea temperatura, presión, caudal o velocidad del motor, los sensores recopilan y transmiten datos en tiempo real sobre el estado actual de los equipos y procesos utilizando protocolos de comunicación como Modbus , HART y Profibus . Los actuadores, a su vez, reciben comandos del sistema de control utilizando los mismos protocolos para ajustar procesos físicos, como abrir una válvula o arrancar un motor, asegurando que el sistema funcione dentro de los parámetros deseados.
2- Controladores lógicos programables (PLC) y sistemas de control de distribución (DCS)
Los controladores lógicos programables (PLC) y los sistemas de control de distribución (DCS) sirven como el "cerebro" del sistema, pero difieren en escala y función. Los PLC, que a menudo se comunican a través de Modbus , Ethernet/IP o Profibus , se utilizan normalmente para control discreto y son ideales para automatizar tareas localizadas, como controlar una sola máquina en una línea de montaje. DCS, que normalmente utiliza OPC-UA , Foundation Fieldbus o Modbus TCP/IP , está diseñado para procesos continuos y supervisa múltiples sistemas interconectados en una instalación más grande, como una planta química. Por ejemplo, mientras que un PLC podría controlar el arranque y la parada de los motores en una línea de fabricación, un DCS gestionaría todo el proceso de producción continua de una refinería de petróleo, garantizando una coordinación perfecta entre varios subsistemas.
3- Unidades terminales remotas (RTU)
Como sugiere el nombre, este componente es común en aplicaciones remotas. Las RTU actúan como centros de datos dentro del sistema SCADA , ubicados en plantas o sitios remotos para recopilar y transmitir datos de sistemas externos como sensores, actuadores y PLC. Las RTU se utilizan en diversas industrias y los protocolos de comunicación que emplean pueden variar según la aplicación específica:
- Fabricación : en entornos de fabricación industrial, las RTU suelen utilizar Modbus RTU o Modbus TCP/IP para una comunicación confiable entre las máquinas y los sistemas de control. Estos protocolos son ampliamente compatibles con dispositivos industriales, lo que permite una integración perfecta con PLC y sensores en la planta.
- Petróleo y gas : para el monitoreo remoto de tuberías, bocas de pozo y refinerías, DNP3 e IEC 60870-5-101/104 debido a su sólido desempeño en comunicaciones de larga distancia y entornos hostiles. Estos protocolos garantizan que los datos se transmitan de manera confiable desde ubicaciones remotas a la sala de control, a menudo a través de amplias áreas geográficas.
- Gestión de agua y aguas residuales : DNP3 y Modbus se utilizan con frecuencia en sistemas de gestión de agua por su capacidad para soportar el monitoreo y control remoto de bombas, válvulas y plantas de tratamiento. La confiabilidad y facilidad de implementación hacen que estos protocolos sean ideales para sistemas distribuidos como instalaciones de agua y aguas residuales.
- Sector energético : la industria energética normalmente se basa en IEC 60870-5-101/104 y DNP3 , que están diseñados para una alta confiabilidad y seguridad en las redes de transmisión y distribución de energía. Estos protocolos admiten el monitoreo en tiempo real de subestaciones, transformadores y otras infraestructuras críticas en grandes redes de servicios públicos.
Las RTU recopilan datos en tiempo real de sensores y actuadores, los convierten a un formato adecuado para sistemas SCADA y los transmiten a un software SCADA central o a una interfaz hombre-máquina (HMI) para su posterior procesamiento y control. Además, las RTU pueden enviar comandos a dispositivos de campo, lo que permite el control remoto de equipos, incluso en operaciones grandes o geográficamente dispersas. Esto hace que las RTU sean esenciales para industrias que requieren monitoreo y control en tiempo real en entornos distribuidos.
3.1 Gateway IoT industrial (opcional)
Los Gateway IoT industriales pueden servir como una adición opcional pero muy valiosa a SCADA . Estas gateway pueden conectarse directamente a cualquiera de los componentes antes mencionados (sensores/actuadores, PLC o RTU) y actúan como un puente entre los equipos industriales y las plataformas basadas en la nube . Por un lado, pueden soportar protocolos industriales como OPC-UA , Modbus , PROFINET , EtherNet/IP y BACnet , asegurando la compatibilidad con una amplia gama de dispositivos y maquinaria. Por otro lado, transmiten datos utilizando protocolos compatibles con la nube como HTTP y MQTT , lo que facilita el intercambio de datos seguro y eficiente entre el taller y la nube. Esta combinación permite la recopilación de datos en tiempo real, el monitoreo remoto y el análisis avanzado, lo que permite a las empresas optimizar las operaciones y aprovechar las soluciones basadas en la nube para el mantenimiento predictivo y la transformación digital.
4- Interfaces Hombre-Máquina (HMI)
Las interfaces hombre-máquina (HMI) sirven como capa interactiva entre los operadores y el sistema SCADA , proporcionando visualización en tiempo real de los datos recopilados de sistemas externos como PLC, RTU y sensores. Las HMI pueden ubicarse en una sala de control centralizada, donde los operadores monitorean y administran toda la instalación, o pueden ubicarse localmente junto a un PLC o proceso específico para el control en el sitio. En configuraciones centralizadas, las HMI permiten a los operadores supervisar las operaciones de toda la planta y emitir comandos de forma remota. En configuraciones locales, permiten a los técnicos interactuar directamente con maquinaria o procesos específicos en la fábrica, ajustando parámetros o respondiendo a alarmas en tiempo real. Esta flexibilidad garantiza que los operadores tengan el nivel adecuado de control, ya sea que administren toda la planta o se concentren en una sola máquina.
5-Software SCADA
Y, por último, las soluciones de software SCADA , como el software Ignition , son las que lo unen todo. Estas potentes soluciones recopilan, procesan y muestran datos de toda la planta, convirtiendo los datos sin procesar en información procesable. A través de análisis de tendencias, alarmas y datos históricos, el software SCADA ayuda a los operadores y gerentes a tomar decisiones para mejorar la eficiencia, reducir el tiempo de inactividad y prevenir problemas antes de que se conviertan en problemas. Es la torre de control de toda la operación, que le brinda no solo una vista de lo que está sucediendo ahora, sino también el análisis predictivo para prepararse para lo que vendrá a continuación.
Cada uno de estos componentes es fundamental para un sistema SCADA . Sin ellos, estarías volando a ciegas en un mundo basado en datos. Juntos hacen que su operación funcione como una máquina bien engrasada con contratiempos mínimos y máxima eficiencia.
Elegir el sistema SCADA adecuado
Elegir el sistema SCADA adecuado para su operación es una decisión que afectará la eficiencia, la seguridad y el crecimiento a largo plazo de su planta. Con tantas opciones disponibles, es importante sopesar los factores clave que afectarán no sólo el rendimiento inmediato sino también la escalabilidad y adaptabilidad del sistema a medida que sus instalaciones evolucionan.
Interfaz de usuario: mantenlo simple
Una de las partes más importantes de cualquier sistema SCADA es la interfaz de usuario (UI). Si sus operadores no pueden navegar por el sistema fácilmente, todas las funciones avanzadas del mundo no importarán. Busque un sistema que tenga una interfaz de usuario limpia e intuitiva, dashboards claros y navegación sencilla. Cuando suenan las alarmas o se necesitan ajustes rápidos, lo último que desea es una interfaz de usuario confusa y desordenada que ralentice la toma de decisiones.
Una buena interfaz SCADA permite a su equipo trabajar de manera eficiente, tomar decisiones en tiempo real y reducir el error humano, todo lo cual es fundamental en entornos de alta presión.
Escalabilidad: prepare su sistema para el futuro
Las operaciones industriales nunca son estáticas. A medida que su empresa crece, su sistema SCADA debería crecer con ella. La escalabilidad es un factor clave a la hora de elegir una plataforma SCADA . Ya sea que esté agregando nuevas instalaciones o líneas de producción, su sistema SCADA debería poder manejar mayores cargas de datos, más sensores y nuevos procesos.
Un sistema que pueda adaptarse a cambios futuros le evitará costosas actualizaciones o reemplazos en el futuro. Piense a largo plazo no sólo en sus necesidades actuales sino también en cómo ve la evolución de su operación en los próximos 5 a 10 años.
Compatibilidad: Integración con Protocolos Industriales
Su sistema SCADA necesitará comunicarse con muchos dispositivos y máquinas en la planta. Es importante elegir un sistema que sea compatible con protocolos industriales comunes como Modbus, DNP3 y OPC UA. Compatibilidad significa que su sistema SCADA puede integrarse con el equipo existente y cualquier tecnología nueva que pueda agregar.
Esta interoperabilidad también permite que su sistema obtenga datos de múltiples fuentes, brindándole una visión integral de su operación. Sin una compatibilidad adecuada, terminará con soluciones costosas y datos fragmentados que ralentizarán la eficiencia operativa.
Seguridad: proteja su infraestructura
A medida que los sistemas SCADA se conectan a la web y a las soluciones basadas en la nube, la seguridad se convierte en una máxima prioridad. Asegurarse de que su sistema SCADA cumpla con los estándares de seguridad requeridos por su departamento de TI no es negociable. Querrá preguntar a sus proveedores potenciales sobre sus protocolos de seguridad, estándares de cifrado, autenticación multifactor y cómo manejan parches o vulnerabilidades.
En el mundo actual, una violación de la seguridad puede ser devastadora, no sólo financieramente sino también para la fuerza laboral y el medio ambiente. Elija un proveedor que haga de la seguridad una parte central de su negocio y no una ocurrencia tardía.
Confiabilidad del proveedor: un socio a largo plazo
Cuando se trata de SCADA su relación con el proveedor no termina después de la instalación. La confiabilidad del proveedor es clave para el éxito a largo plazo de su sistema. Quiere un proveedor con un historial comprobado de sostenibilidad y atención al cliente. Deberían estar disponibles para ayudarle con actualizaciones, resolución de problemas y ampliaciones del sistema.
Investigue la reputación del proveedor en la industria, observe estudios de casos y solicite testimonios. Un proveedor confiable será un socio que lo ayudará a evolucionar y mantener su sistema SCADA en los años venideros.
Presupuesto: planificación para el crecimiento sin excesos
Si bien es fácil optar por el sistema SCADA más avanzado que existe, es necesario equilibrar su presupuesto con las necesidades de su planta. Algunos sistemas pueden tener características excesivas para operaciones más pequeñas. Optar por un sistema complejo y costoso le obligará a incurrir en costes innecesarios.
Tenga cuidado también con los costes ocultos, especialmente los servicios profesionales. Los proveedores pueden cobrar extra por modificaciones o ampliaciones. Obtenga una comprensión clara de cuánto costarán los servicios continuos para poder presupuestarlos. Planificar el crecimiento sin comprometerse demasiado con un sistema que se volverá demasiado costoso con el tiempo es clave para ser ágil y evitar la dependencia de un proveedor.
Elegir el sistema SCADA correcto es una gran decisión, pero con una planificación cuidadosa y considerando estos factores estará preparado para tomar una decisión que impulse la eficiencia operativa, proteja sus datos y escale con su negocio.
Opciones de software SCADA
SCADAIgnition : la opción moderna y flexible para los fabricantes
Ignition SCADA se ha convertido en una solución SCADA moderna para los fabricantes por su flexibilidad y arquitectura abierta. A diferencia de los sistemas SCADA tradicionales, Ignition tiene etiquetas, clientes y conexiones ilimitadas para que usted obtenga la escalabilidad que necesita sin costo. Su moderna interfaz basada en web permite el acceso desde cualquier dispositivo, datos en tiempo real y control al alcance de su mano. El diseño modular significa que puede comenzar poco a poco y crecer según sea necesario, integrarse con sistemas y protocolos existentes, por lo que es la opción flexible para los fabricantes que buscan preparar su operación para el futuro.
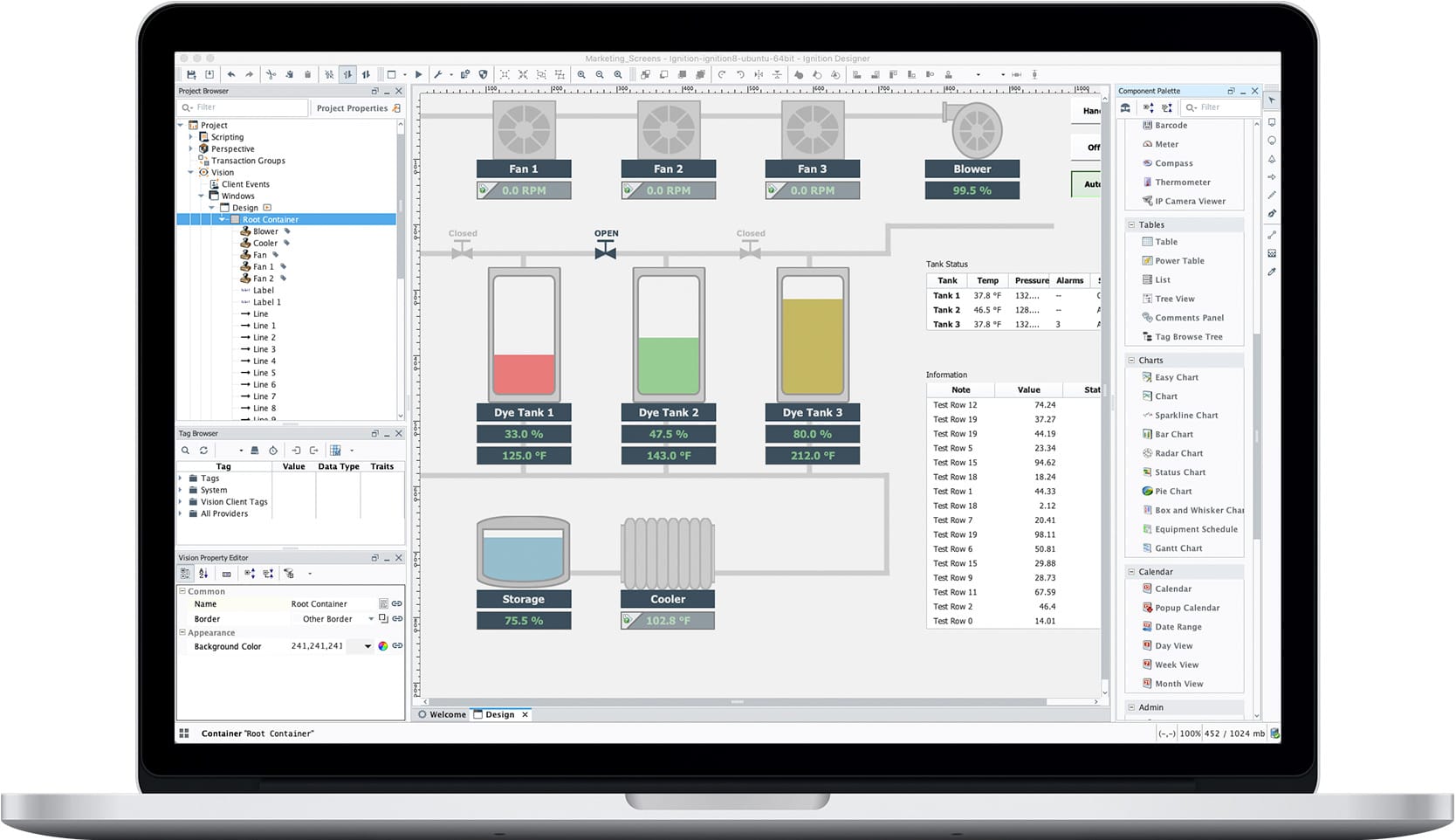
Siemens SCADA - Simatic WinCC: Avanzado para industrias complejas
Siemens SCADA, particularmente Simatic WinCC, es de alto rendimiento, monitoreo y control en tiempo real, por lo que es perfecto para industrias grandes y complejas. Desde productos farmacéuticos hasta energía, los sistemas SCADA de Siemens ofrecen una precisión incomparable con una amplia funcionalidad para visualización de procesos, adquisición de datos y mantenimiento predictivo. La integración de Simatic WinCC con los productos de automatización de Siemens crea un entorno perfecto donde los PLC, HMI y SCADA se comunican entre sí. Para plantas donde el tiempo de actividad es crítico y el tiempo de inactividad puede costar millones, Siemens SCADA ofrece confiabilidad y funciones avanzadas para optimizar incluso las operaciones más complejas.
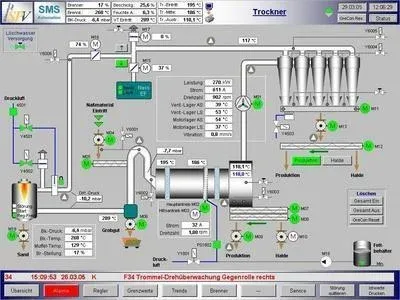
Schneider SCADA: una alternativa integral
Schneider Electric ofrece un sólido conjunto de soluciones SCADA y telemetría, que ofrece componentes de hardware y software para optimizar el control y la supervisión. Su gama de hardware incluye unidades terminales remotas (RTU), controladores lógicos programables (PLC) y gatewayde comunicación, que están diseñados para integrarse perfectamente en entornos industriales existentes. En cuanto al software, Schneider ofrece plataformas SCADA avanzadas como EcoStruxure, que permiten la adquisición de datos en tiempo real, el monitoreo remoto y el análisis predictivo, lo que permite a las empresas optimizar las operaciones al tiempo que mejoran la gestión de la energía y la sostenibilidad. Con estas soluciones integrales, Schneider puede ser un socio confiable para los requisitos actuales y futuros.
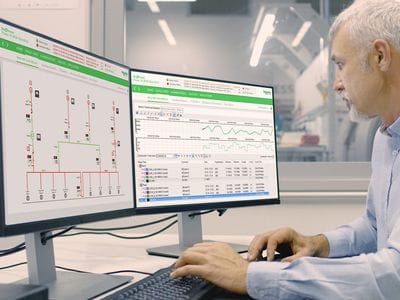
Wonderware SCADA: probado para control de supervisión
Wonderware, que también está en la cartera de Schneider Electric tras la adquisición de Invensys en 2014, tiene un largo legado en el suministro de soluciones SCADA confiables para una amplia gama de industrias. Wonderware se ha convertido en una plataforma confiable en sectores como el ensamblaje de automóviles, alimentos y bebidas, energía y gestión del agua. La adaptabilidad de Wonderware y su facilidad de integración con sistemas industriales lo convierten en una solución ideal para mejorar la eficiencia operativa y la confiabilidad.
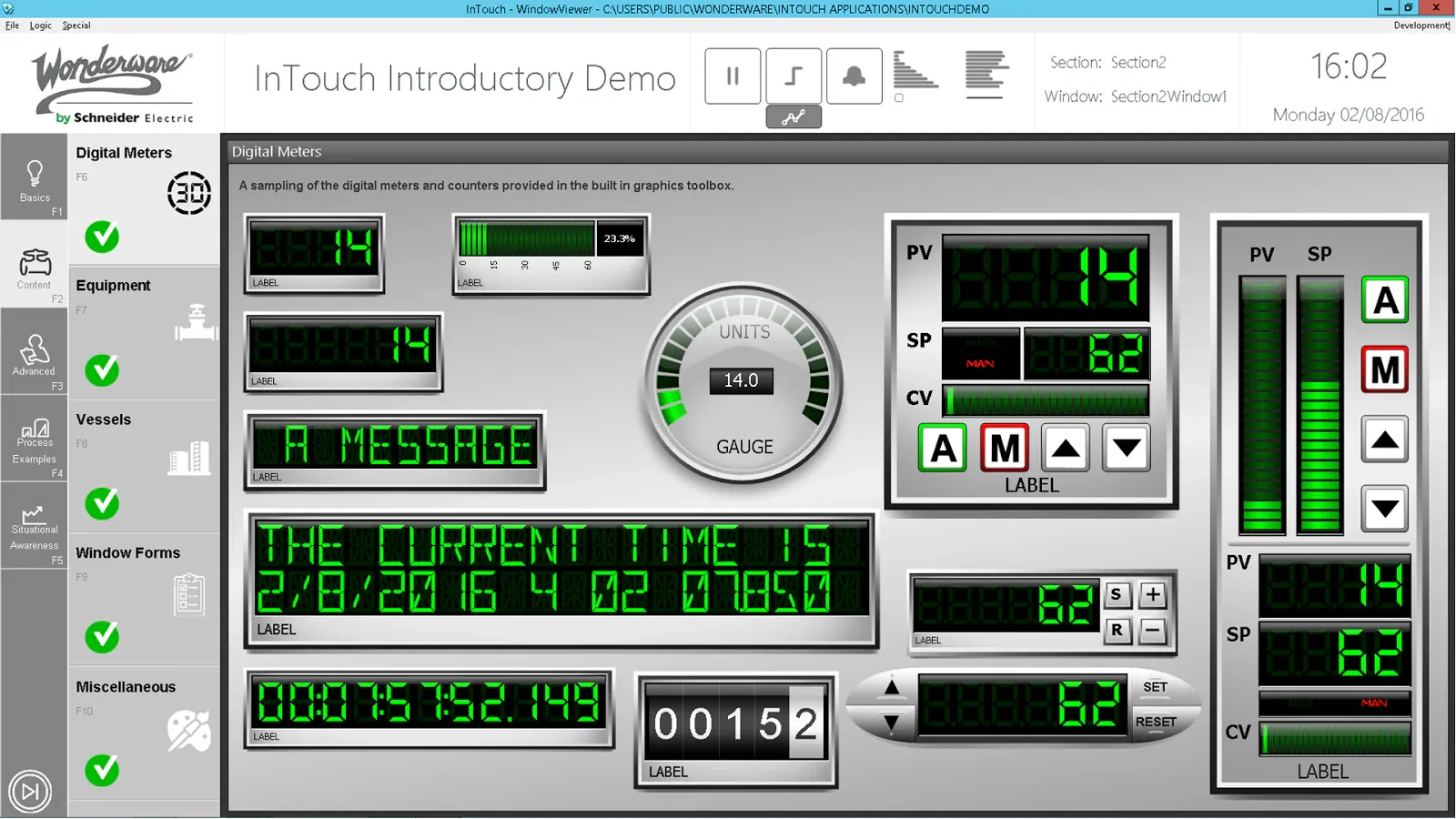
SCADA AVEVA: SCADA en la nube para la Industria 4.0
SCADA AVEVA se ha establecido como líder en soluciones SCADA basadas en la nube, impulsando la transformación digital en todas las industrias. En 2023, Schneider Electric adquirió AVEVA, lo que fortaleció la cartera de Schneider para ofrecer soluciones de fábrica inteligentes. Con su enfoque de dar prioridad a la nube, AVEVA permite el monitoreo y control remotos, lo que permite a las empresas optimizar las operaciones desde cualquier parte del mundo. Industrias como la energía, el petróleo y el gas y la gestión del agua confían en el software SCADA de AVEVA para aumentar la eficiencia y la sostenibilidad.
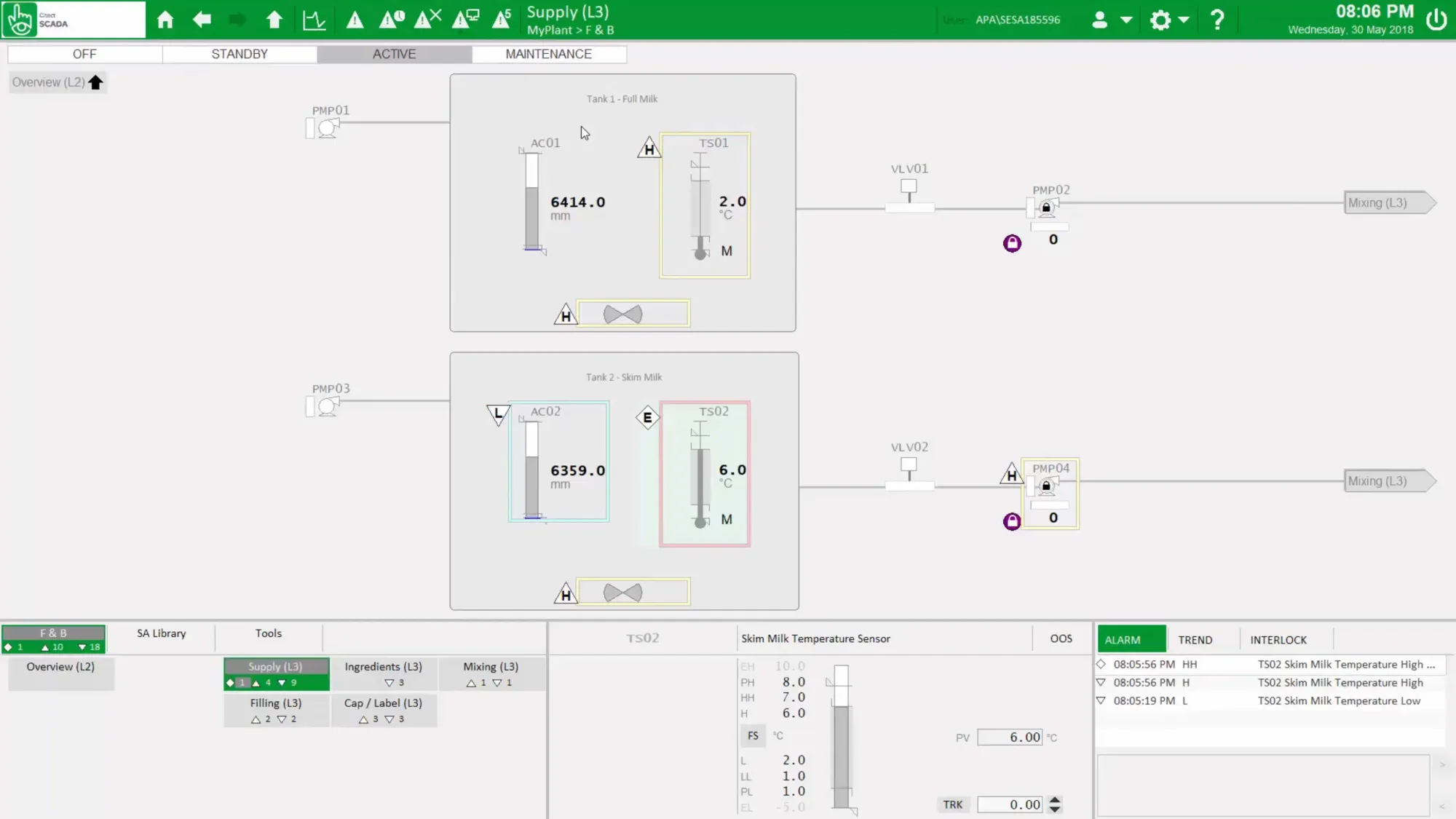
VT SCADA: un nombre para monitoreo y control remotos
Aunque es un actor más pequeño, VT SCADA ha ganado participación de mercado en industrias que requieren monitoreo y control remotos sólidos, entre otros. Su modelo de licencia simple y su rendimiento confiable lo convierten en una opción popular para plantas de tratamiento de agua, oleoductos y servicios públicos. VT SCADA está diseñado para una alta disponibilidad con características como redundancia integrada y conmutación por error automática para que los sistemas permanezcan activos incluso en condiciones difíciles. Puede ejecutarse en entornos remotos y distribuidos con un mantenimiento mínimo, por lo que VT SCADA es la mejor opción para industrias donde la visibilidad remota en tiempo real es fundamental para la continuidad del negocio.
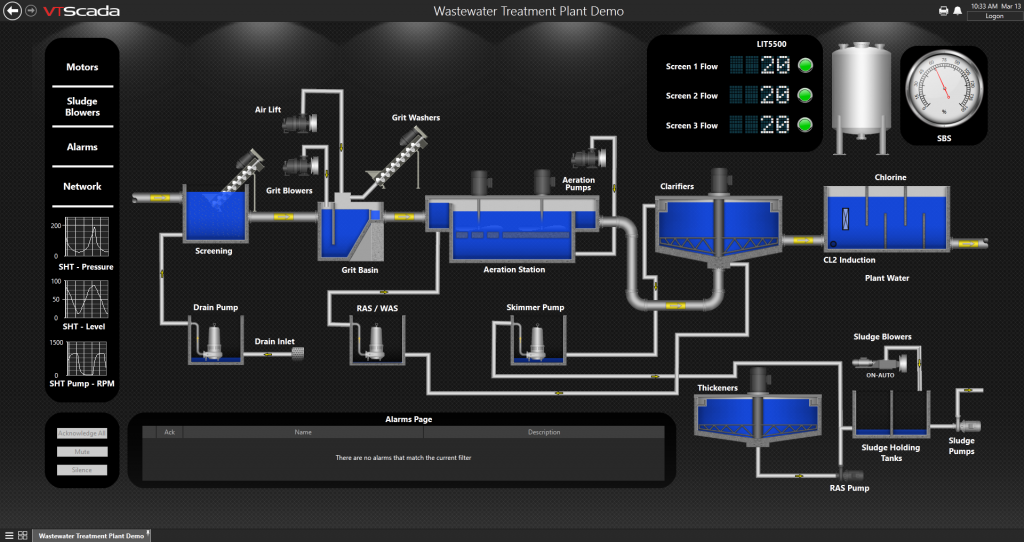
Conclusión
Escalabilidad y flexibilidad: las claves de la transformación digital
En el cambiante mundo industrial actual, la escalabilidad y la flexibilidad son más que simples palabras: son la base del crecimiento. Un SCADA que puede escalar con su operación significa que no estará atrapado en tecnología antigua cuando su negocio crezca. Ya sea agregando nuevas líneas de producción, más dispositivos IoT o flujos de datos complejos, un SCADA debería poder manejar demandas crecientes sin sudar. La flexibilidad también es clave ya que cada industria es diferente. La capacidad de personalizar el sistema según su flujo de trabajo operativo e integrarlo con los protocolos existentes es la clave para preparar su estrategia de automatización para el futuro.
SCADA en la nube: El complemento perfecto para los sistemas SCADA tradicionales
Cloud SCADA ya no es un concepto: se está convirtiendo en la nueva norma en el mundo industrial. Con acceso a datos en tiempo real desde cualquier parte del mundo, SCADA en la nube proporciona una flexibilidad operativa sin precedentes. La nube elimina la necesidad de infraestructura local, lo que reduce los costos de mantenimiento y aumenta la escalabilidad. crezca el Internet industrial de las cosas SCADA dominará ofreciendo más seguridad, una integración perfecta con otras herramientas digitales y la agilidad para enfrentar los desafíos de fabricación modernos. Para los profesionales de confiabilidad que buscan estar a la vanguardia, la transición a un SCADA podría ser el siguiente gran paso para optimizar tanto la eficiencia como la competitividad.